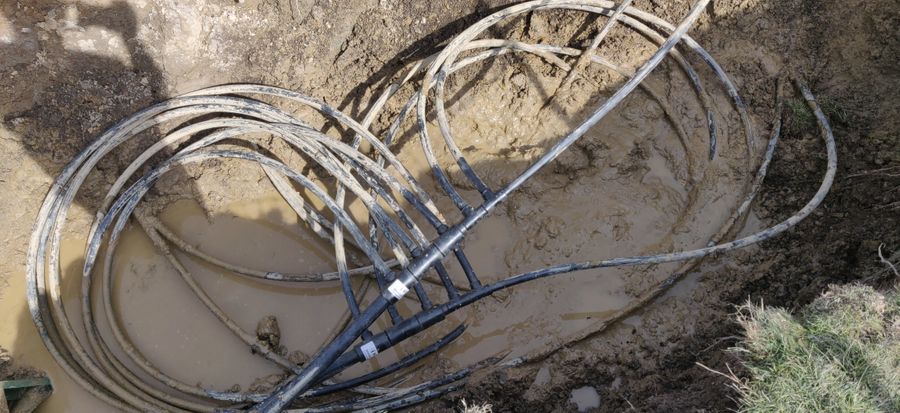
Less burning of the benjamins
When we looked at the house, one of the first things we knew we'd be changing was the HVAC system... well I should say heating system, because the house doesn't have AC. The house has a pellet stove and a fuel oil furnace - along with a nice big 300 gallon red tank in the basement. One of the first things we did in the new house was schedule HVAC contractors to get price quotes. We got quotes for heat pumps with electric backup, heat pumps with propane backup, AC with fuel oil as well as two geothermal systems. After much debate, but only after being in the house for 1 month (Aug 2020) we decided to go with a geothermal system - one that would also heat our hot water. While a costly system, we hoped the decrease monthly costs would allow us to recoup the up front cost; plus the 26% tax credit helps offset it as well.
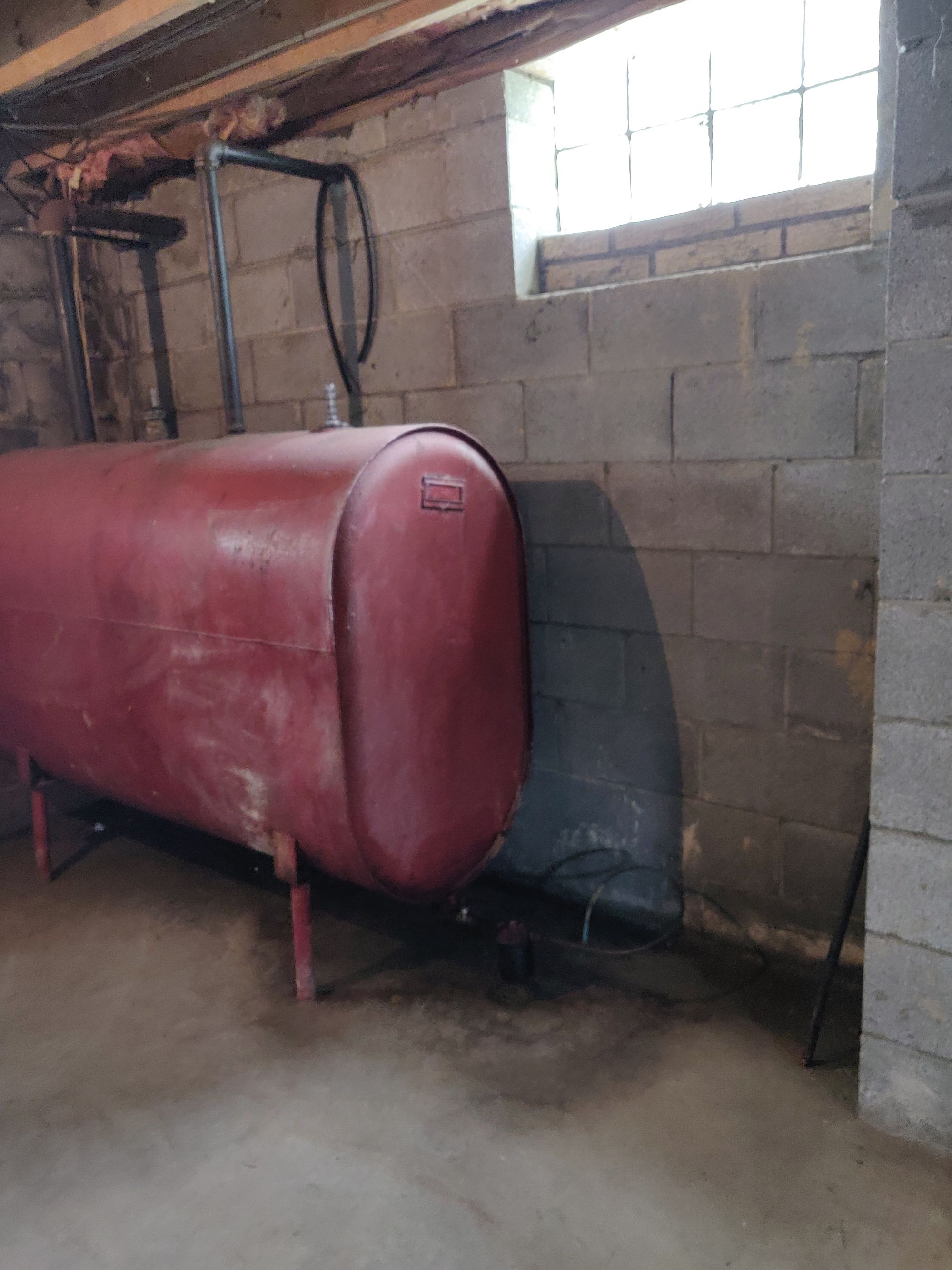
The contractor said the installation would likely occur in December; knowing this we decided to try and make do with a partial tank of fuel oil and wood pellets for our heating for the first part of winter. We only wanted a partial tank so that we were sure that it would all be used and it was one less thing to deal with when it came time to pay somebody to remove the fuel oil tank. December rolls around and due to bad weather and a few jobs that took longer, our install was now going to happen in January. Luckily the weather wasn't still too bad and we still had some fuel oil, so we turned the furnace down a bit and relied on the wood pellet stove a bit more. The install date in January rolls around, and it was pushed back yet again.. however this we weren't as lucky - we had run the fuel oil tank empty. Uh Oh!
Fuel oil tanks, like any liquid tanks can develop sludge and debris over the years; and as long as one doesn't run the tank empty, the sludge just stays at the bottom and doesn't cause any issues with the filters & pump.. However, our tank was pretty empty when we moved in and after the first fill the sludge actually killed the fuel pump. We had a contractor come out at the time to fix it - this was right after we spent $300 getting a partial tank, so it was definitely worth it.
Since the tank was empty again we knew it could have an issue and we didn't want to pay for a full tank just to need to have a contractor fix the fuel pump again. Instead, we dumped in 10 gallons of diesel and hoped the furnace would work. Turns out it didn't like something and I wasn't able to get it to work, even after manually priming the pump. So now we had to decide, pay a contractor to come out and fix the fuel pump and then for a full tank or just use wood pellets. We decided on wood pellets, because at this time, the install was still only a few weeks away. Since I'm not afraid of electicity and most blowers are simple motors that need power, I figured out how to hook the furnace blower to power so that it was always on; this way at least the heat from the pellet stove would be blown around the house as there's an intake in the same room.
It turns out that when the outside temperatures are sub-freezing and while a wood pellet stove can keep a decently large space warm - though it needs needs 3 or 4 bags of pellets per day to do so - it doesn't keep a whole house warm. We supplemented the wood pellet stove with some space heaters and a portable ac/heater unit. The house was comfortable.. but it wasn't cheap. A bag of wood pellets runs for around $5 depending on where you get it and the quantity.. so 3 bags a day plus at least one 1500 watt space heater meant we were spending between $25 and $30 per day heating the house.. the majority of which was literelly turning into fire.
Sadly, it wasn't a short delay from the January date.. the install was finally scheduled to begin monday March 1st! The friday before they dropped off excavator and discussed exactly what the plan was for where things were going. Geothermal HVAC are very similar to a conventional heat pump/AC system, but instead of exchaning heat using a fan and coil outdoors, they exchang heat with the ground - using a water loop of some sort. Our system uses horizonal loops, which meant they had to lay 1200' of pipe (6 loops of 2') underground. Luckily they didn't have to tear up our whole yard - they were able to use a horizontal boring machine to lay the loops.
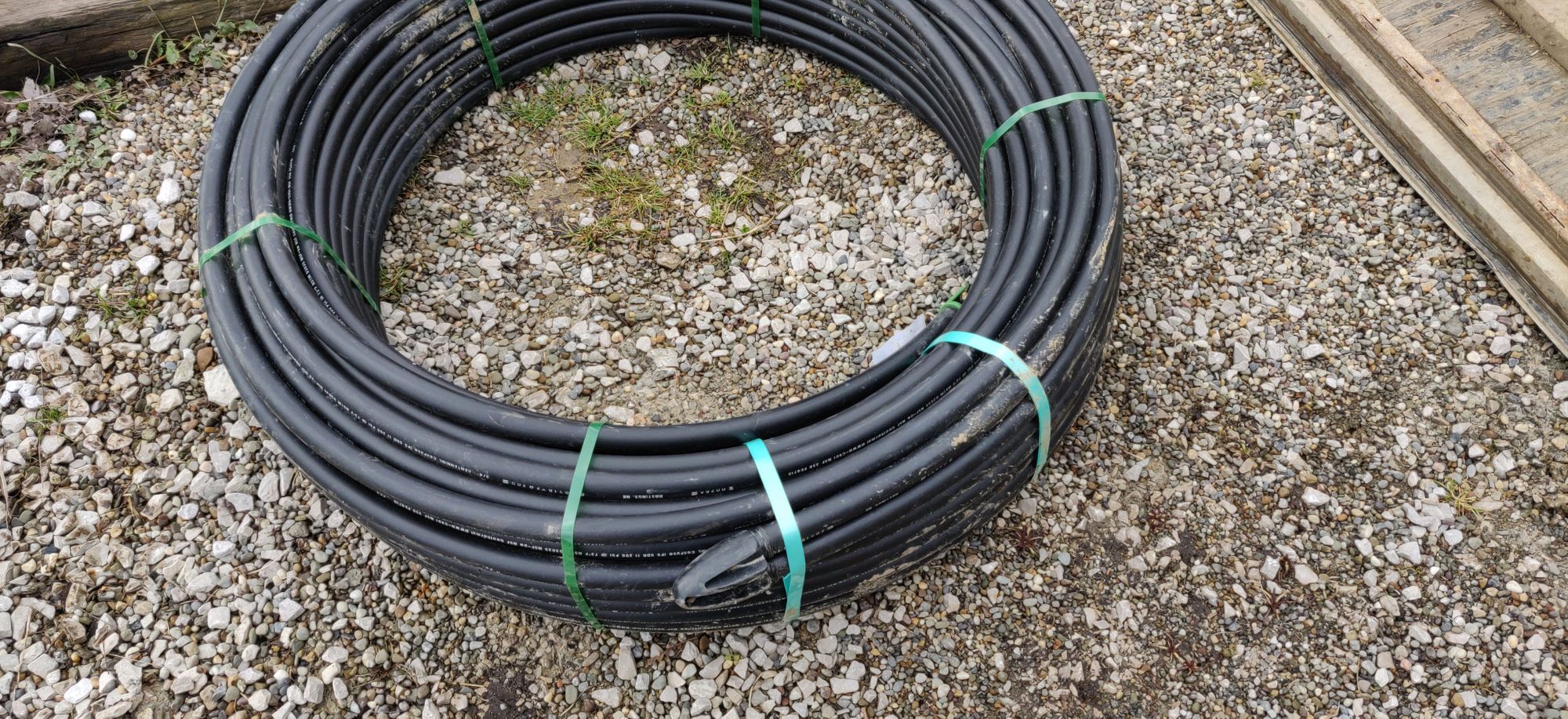
Each loop consists of two 3/4 HDPE pipes, with a fitting on one end that connects them together and the other two ends that connect to two different manifolds.
They started by digging a big pit for where the manifolds will go and each loop with "start". Then they take the boring machine, bore into the ground, then go through the pit and continue about 250'. The reason they continue is the machine can only slightly curve the direction so it slopes down to the desired depth (8-12') then they keep it flat for ~200' feet. Then the have it rise again so it pops out of the ground. They then attach the open ends of the loop to the "drill bit" and pull it back through the hole they just made.
One thing this drilling needs is lots of water - about 250 gallons per loop. Luckily we hadn't filled in the toddler-death-trap well yet, and they were able to use it along with the other old well for their water; though they had to take a day off because their wasn't enough water available. We watched the bit pop up out of the ground for the first loop, right underneath Daniela; luckily she didn't get wet!
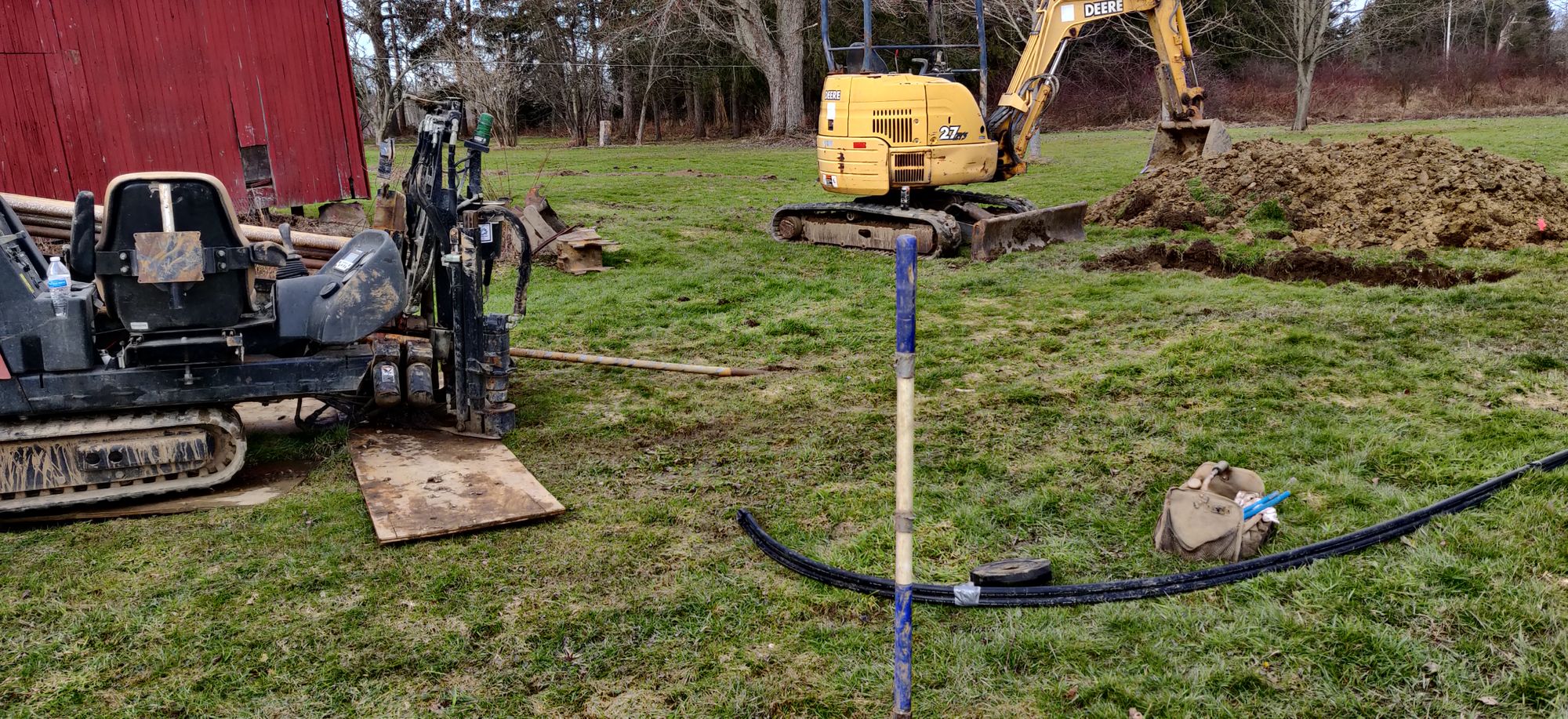
They repeated the process 6 times - with each loop fanning out from the pit about 15 degrees away from the previous.
Once they had all 6 loops in the ground they pressure tested them individually. Once they all passed it was time to lay the pipes to connect them into the house. This meant they had to dig a pit next to the house and pull a larger set of pipes through. Which is basically the same process except they pull back two bigger pipes.
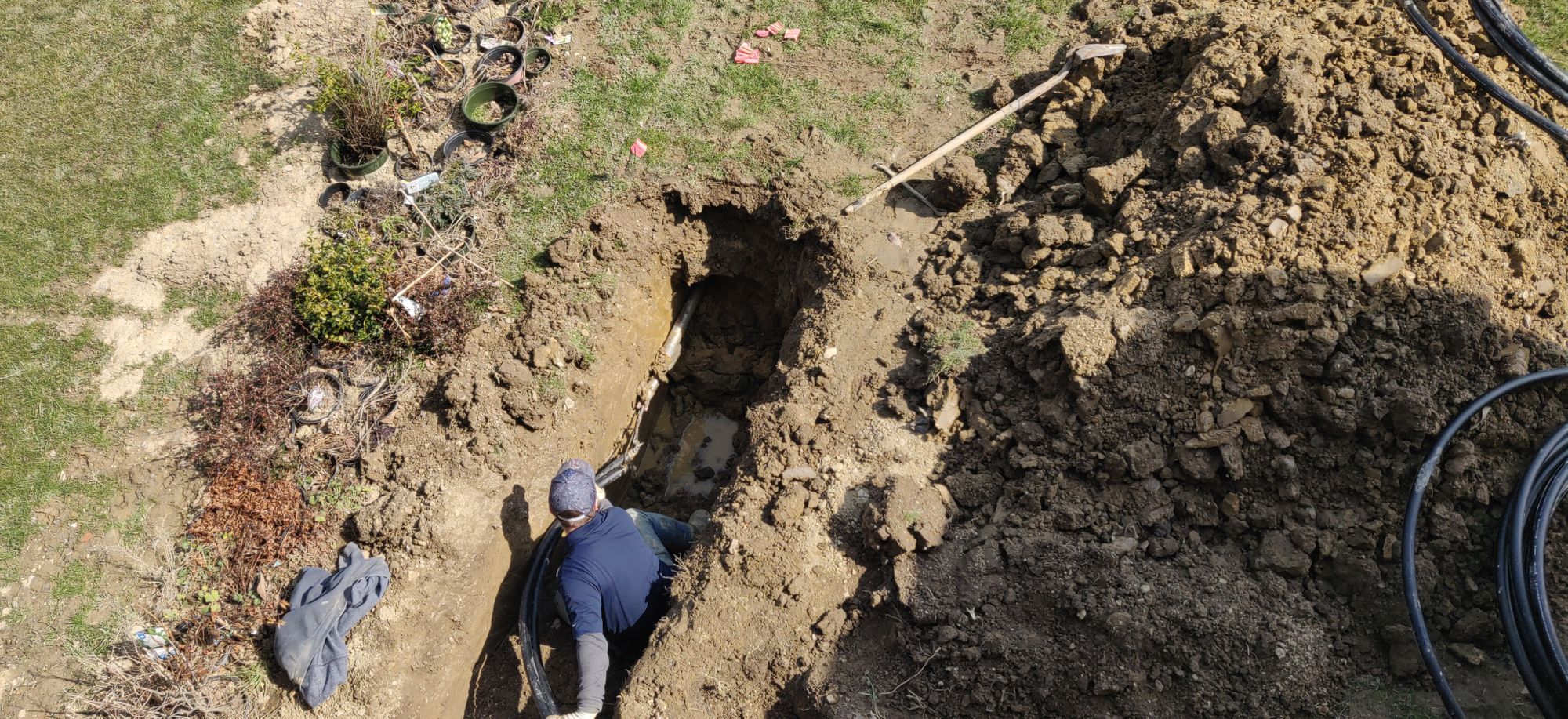
Once the larger pipes were in the big pit, they used heat welding to join the pipes - no solvents here. This is to ensure the system is completely maintainence free for life.
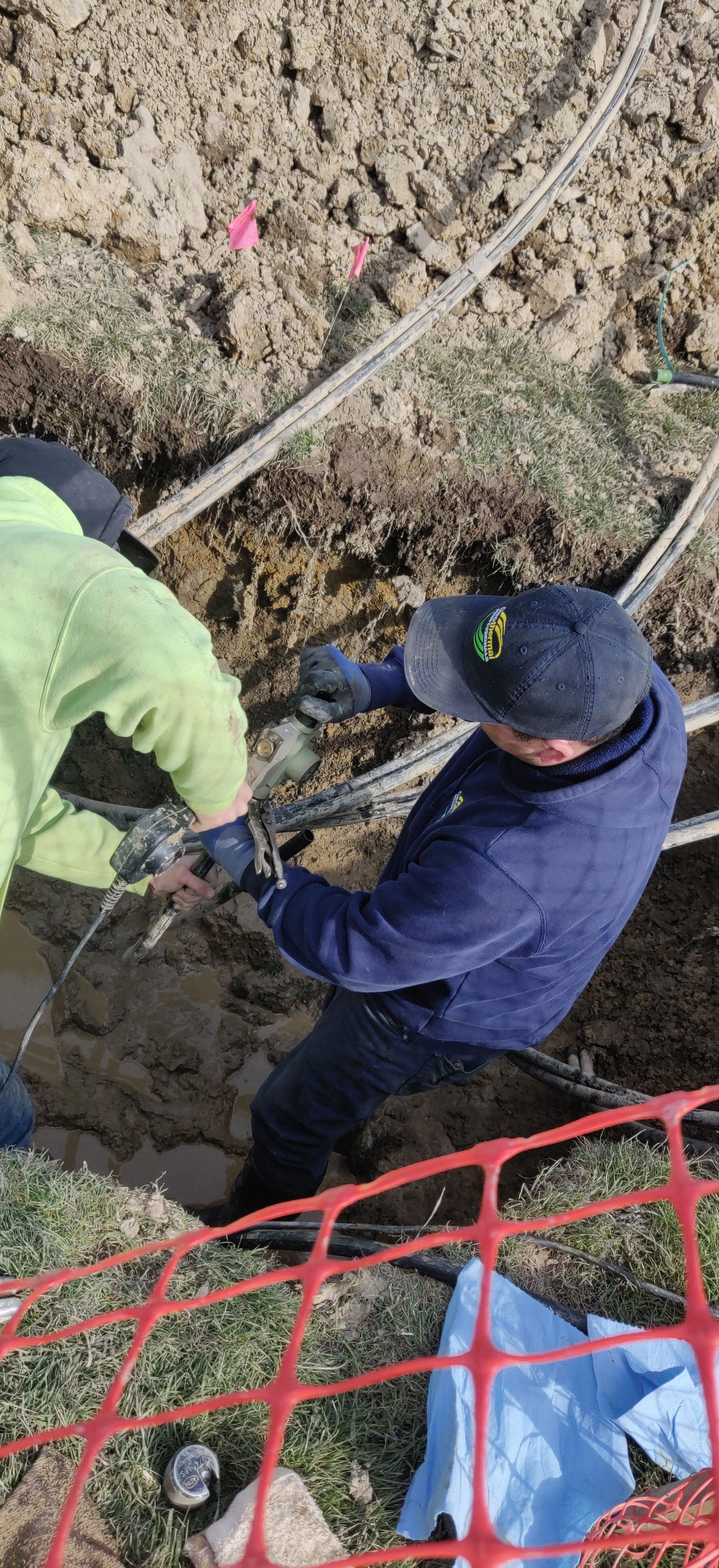
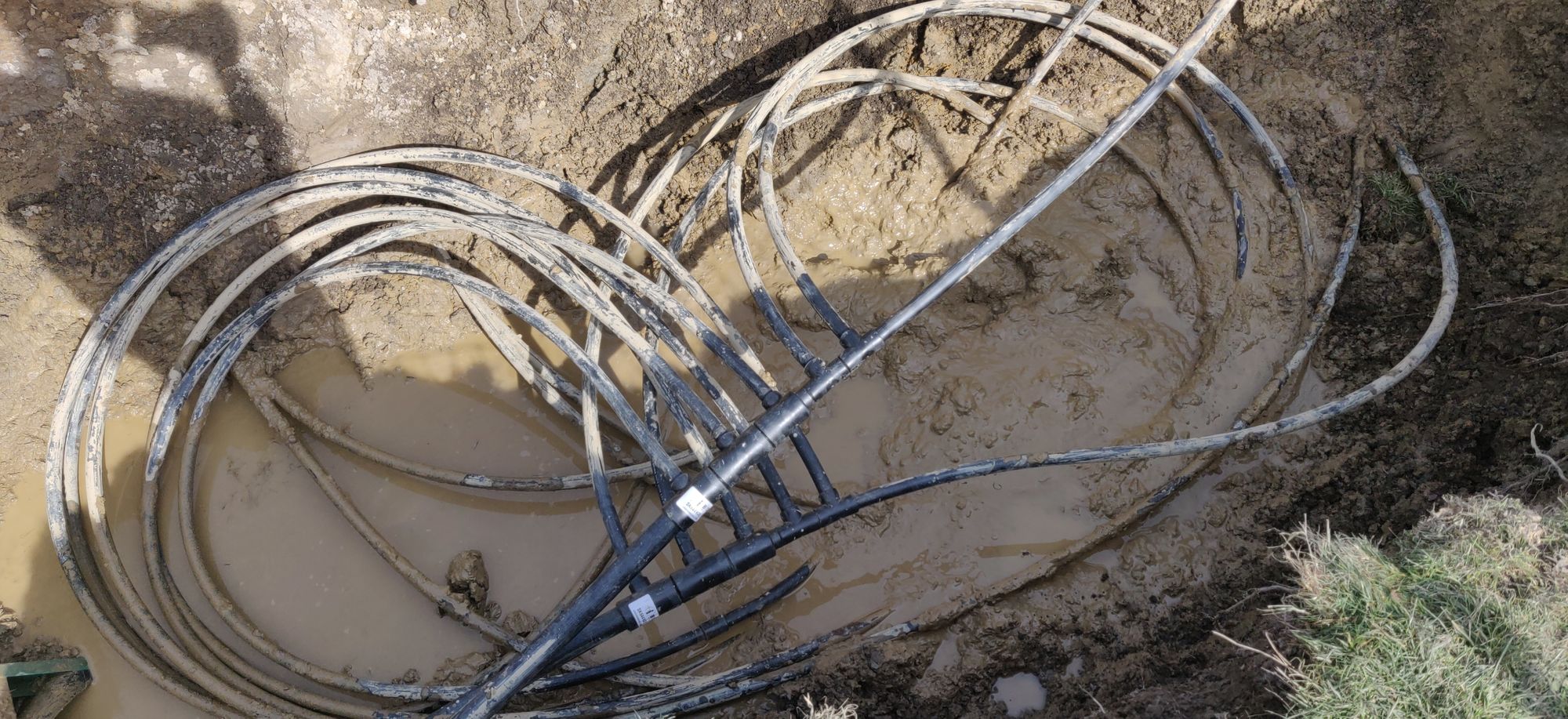
Once the manifold was in, they pressure tested the entire system, drilled a pair of holes into the house, fed the pipes through with PVC sleeves, added some hydraulic cement, backfilled everything and were done with the loop instalation.
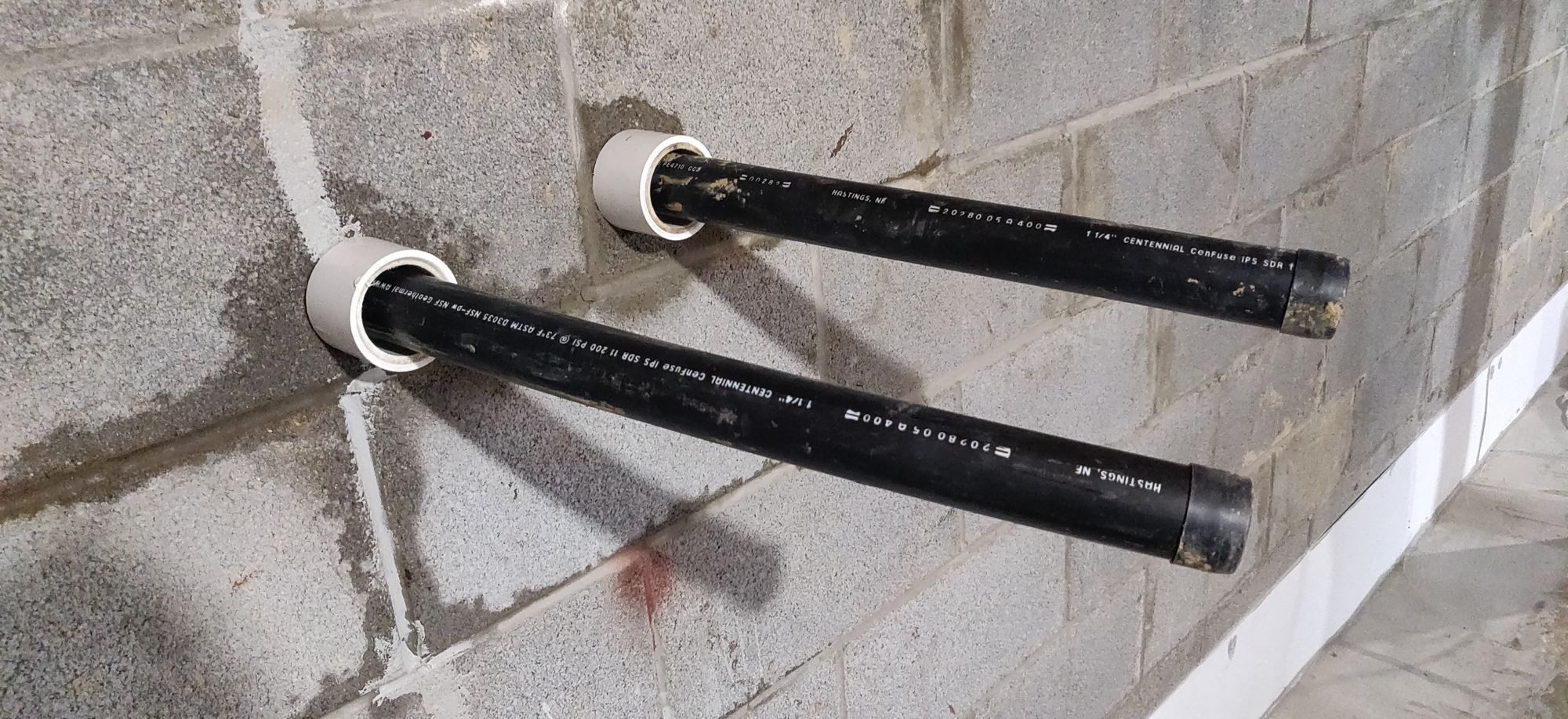
Interior system is still TBD.. scheduled for later this week.